Cold? Naturally!
Sustainable and efficient - two keywords that have had a decisive impact on our time and have gained in relevance in recent years, especially in refrigeration. Increased environmental awareness in society and industry has therefore led to a kind of renaissance of natural refrigerants, especially CO2. This is a trend that is being driven to a considerable extent by the European Union's F-Gas Regulation. Wieland supports this turnaround with a tube system that meets the high requirements for the use of CO2.
In refrigeration, especially in the area of supermarket refrigeration systems, ecologically oriented plant concepts are increasingly being used today. "The increasingly important environmental aspect is the driving factor here", explains Matthias Boehringer, Head of Application Engineering at Wieland, "classical synthetic refrigerants are usually characterized by a high global warming potential (GWP). The new F-gas regulation, which successively imposes bans on refrigerants with high GWP, is one reason why CO2 as a refrigerant has come back into the focus of many of our customers". Good thermophysical properties, an ozone depletion potential (ODP) of 0 and a GWP of 1 make CO2 a very attractive refrigerant. It is a naturally occurring substance and occurs abundantly in the atmosphere. At the same time, certain conditions should be considered when using CO2: "High operating pressures, typically between 80 and 130 bar, are required to ensure efficient operation of CO2 plants," says Boehringer. High demands are therefore placed on the tubes and heat exchangers, for which K65 and the associated K65 tube system have been specially developed.
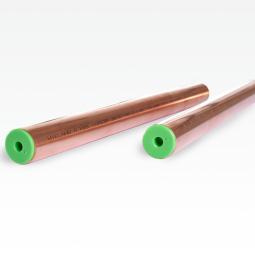
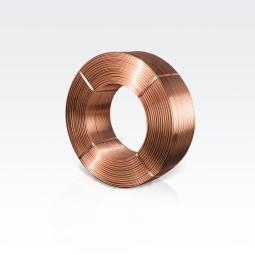
Creative application for a material with originally different application
10 years ago, Wieland launched a tube system for high-pressure applications made of the Wieland material K65. "This was driven by enquiries from customers who came to us due to the revitalization of the refrigerant CO2 and were looking for an alternative to normal copper," explains Boehringer. Due to the necessary high pressures, common tubes were very thick-walled, a solution was required that would enable material and cost savings. Wieland went in search of materials and found what it was looking for in K65. "The alloy had already been used in the automotive industry. At that time, Wieland already had a lot of experience in the production of this alloy", Boehringer explains, "the use of the material in the air-conditioning industry was completely new".
A sustainable solution for new and existing plants
K65 enables a economical and safe installation of refrigeration systems with up to 130 bar operating pressure. It is particularly suitable because on the one hand it has a much higher strength than the standard Cu-DHP used, but at the same time it can be deformed to such an extent that customers can continue to use existing production systems. "That was one of the most important criteria, because you can't force an entire industry to set up completely new production lines," says Boehringer. Existing plants can therefore process K65 tubes with minor adaptations. Due to their high strength, they can be constructed with low wall thicknesses. This not only saves material, but also weight and thus facilitates handling during assembly.
The K65 system at a glance
- Cost reduction through reduction of weight per meter
- Very good heat transfer properties
- Reliable joining technique: Soldering instead of welding!
- Economical and safe solution for new and existing refrigeration systems with up to 130 bar operating pressure.