Welding replaces soldering – For more stability and measuring accuracy
Improve your battery management with Wieland-Shunts
The new contacting technology from Wieland enables a direct connection between PCBs and shunts, without soldering and with direct contacting of the resistance alloy. Specially developed contact elements are used to connect the shunt and the printed circuit board of the battery management system (BMS) by means of a welding process. The current is measured directly at the resistance alloy, without any negative influence from copper in the measuring area. The nominal resistance of the shunt is measured after all components have been connected and can then be used to initialize the BMS. This results in better measurement accuracy in all operating states and improved information on SOC and SOH of the connected battery modules.
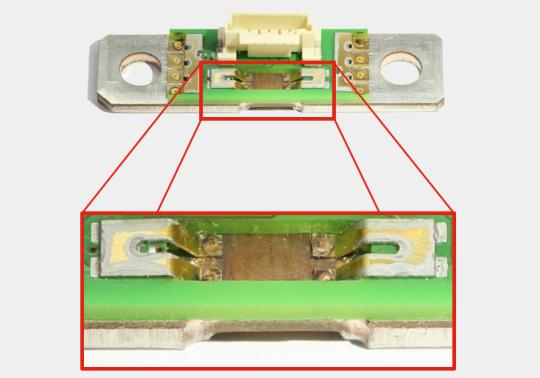
The new shunt contacting technology from Wieland
Contacting the resistor material makes it possible to eliminate large parts of the material-related and temperature-dependent change in resistance (TCR). This does not affect the design of the shunt and the nominal resistance can still be set according to individual customer requirements.
The new contacting technology can be used regardless of the size and structure of the BMS. The contact elements can be integrated into any layout, reducing the number of soldering operations required in production and simplifying the manufacturing processes.
To connect the shunt with a BMS, it usually must be connected to a printed circuit board using a soldering process. This soldered connection can only be made on the surface of the copper terminals. If the shunt heats up due to high currents or external influences, a material-related temperature-dependent change in resistance occurs. By using the new contacting technology, the TCR change in resistance can be reduced, improving the measuring accuracy of the BMS which is connected to the shunt.
Did you know that the temperature-dependent change in resistance of copper can be more than 1000 times higher compared to Wieland resistance alloys? The shunt and BMS can only be connected by soldering via the copper terminals. To enable precise current measurement over a wide temperature range, the influence of copper in the measuring section must be eliminated. This is the only way to reduce measurement tolerances and make use of the available battery capacity.
The high mass of the shunt often means that the soldering process can only be designed very inefficiently. This results in poor cycle times and high material and resource consumption. In addition, in-process inspection possibilities of the soldered connection are very limited.
How it works - Precise current measurement with Wieland-Shunts
Shunt-based current measurement is a widely used method for measuring current in high-current applications. A shunt resistor always consists of copper terminals for connecting busbars and a resistance alloy welded in between. This design ensures a low temperature-related change in resistance (TCR effect), good long-term stability and therefore stable measurement throughout operation. The stability of the resistor is essential to ensure a long life of all components directly connected to the shunt.
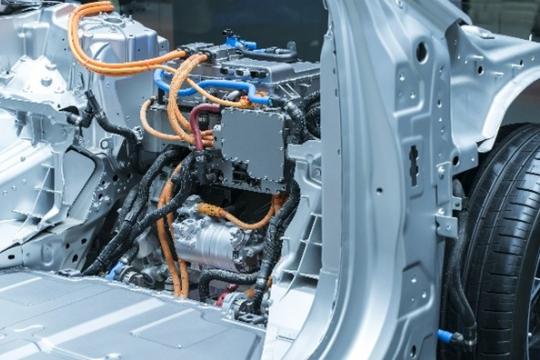
Shunt-based current measurement in an electric vehicle
During charging and discharging, the shunt can measure the current that is currently flowing into or out of the battery. The current is calculated in a BMS using Ohm's law. This allows the battery's State of Health (SOH) and State of Charge (SOC) to be monitored and evaluated.
In an electric vehicle, these are the values of the usable battery capacity and the remaining range of the car. The less accurate the current measurement by the shunt, the more safety buffer must be considered for the SOC and the range specification. The remaining range displayed to the driver decreases and the full battery capacity cannot be used.
Your next steps
Integrate the new contacting technology from Wieland into your battery management system now and improve the performance of the battery modules connected to it.
Please contact our product experts for more information:
emobility@wieland.com