Shell and tube heat exchangers
Our range of products
Our shell and tube heat exchangers at a glance.
Our complete product range
To show the product portfolio of a specific location, please select the company:
Dry Expansion Evaporators
Flooded and Spray Evaporators
Condensers
Oil Separators
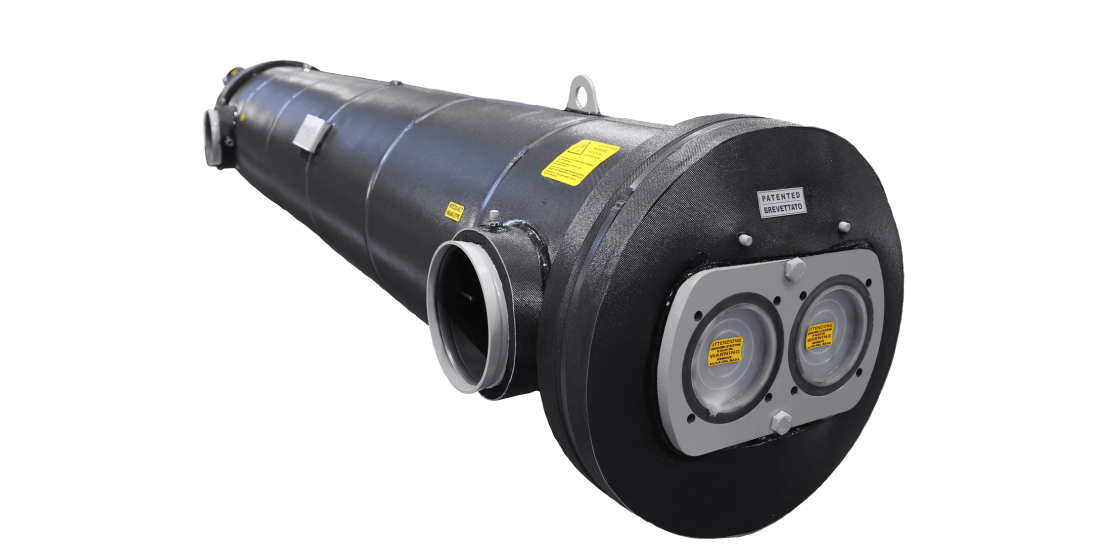
Compact sizes, standard sizes – Up to 4000 kW!
Our dry expansion evaporators guarantee the best performance
- Internally finned tubes are optimized for flow boiling: high exchange coefficients are obtained with relatively low pressure drops.
- The refrigerant distribution system allows the tube bundle to be fed uniformly.
- Solid and customized construction based on project conditions.
- Possibility of construction with Cu-DHP copper bundle, CuNi90 / 10 cupronickel, 316L stainless steel.
- Wide range of sizes: diameters from ø194 mm to ø660 mm, lengths from about 1500 to 4085 mm.
- Available optionals: elastomeric foam insulation, electric heaters, pressure gauges, water filters.
Single-pass counter-current evaporators
In these evaporators, the counter-current configuration optimizes the temperature profile between the two fluids, in order to obtain the maximum local heat exchange coefficient and facilitate the achievement of the desired superheat on suction.
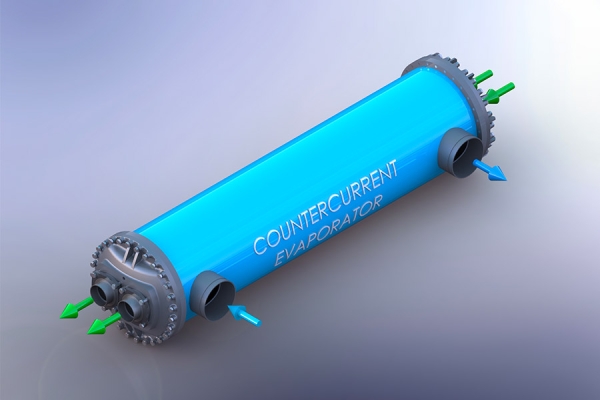
- Powers from 50 kW up to 2500 kW
- Temperature approach up to 2K
- Up to four refrigerant circuits
Countercurrent Evaporator 194.pdf
Countercurrent Evaporator 273.pdf
Countercurrent Evaporator 324.pdf
Countercurrent Evaporator 406.pdf
Countercurrent Evaporator 508.pdf
Countercurrent Evaporator 660.pdf
U-Tube bundle evaporators
In these evaporators the refrigerant flows in a bundle of U-shaped tubes; the refrigerant connections are therefore on a single head. Optimized for R410A, R32, R452B, R454B or for low temperature operation, the EV.U guarantees optimal mass flows, such as to guarantee oil return even with scroll compressors.
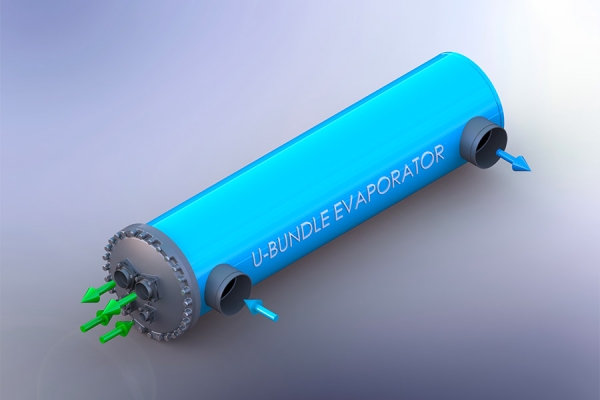
- Powers from 50 kW up to 2200 kW
- Temperature approach up to 2-2.5K
- Up to four refrigerant circuits
- Higher mass flows (minimum partialization for lower circuit)
- Design pressure up to 50 bar
U-Bundle Evaporator 194
U-Bundle Evaporator 219
U-Bundle Evaporator 273
U-Bundle Evaporator 324
U-Bundle Evaporator 559
U-Bundle Evaporator 667
Heat Pumps
Dry expansion evaporators can also be used in condensing mode, for heat pump and/or refrigerant cycle inversion systems. The good efficiencies and the versatility of configuration make them excellent alternatives where you want to standardize the layout of the exchangers in low and high pressure circuits. Available with design pressures up to 50 bar and temperatures up to 150° C, Wieland Provides heat pumps are in step with the market needs for low GWP refrigerants or natural refrigerants, such as the increasingly used propane.
You need more information? Contact us!
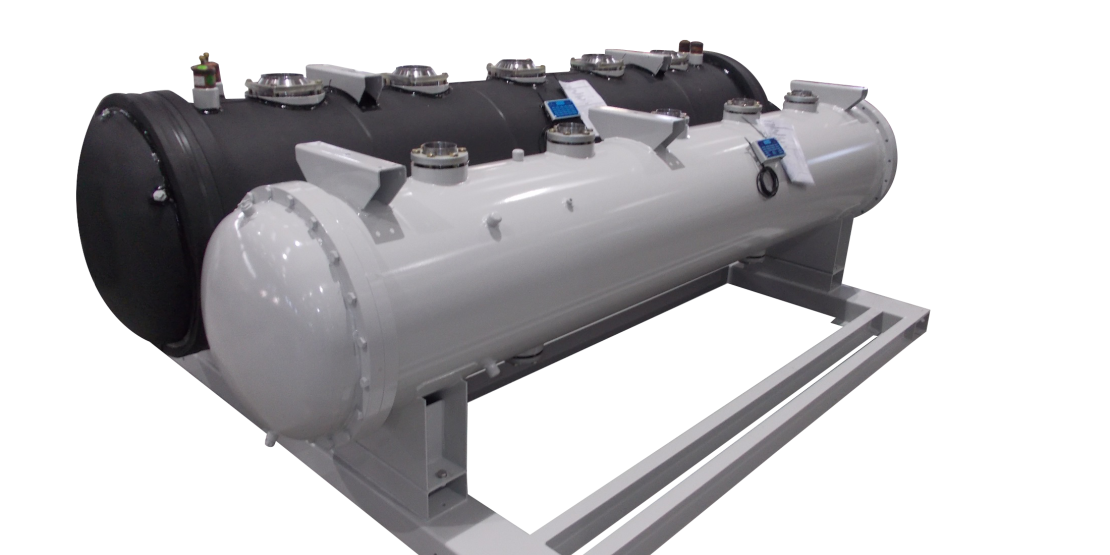
The highest efficiencies with the lowest refrigerant charge – Over 10000 kw capacity available
Complete range of standard flooded evaporators
With integrated internal heat exchange good for guaranteeing high superheat and subcooling
In flooded evaporators, the refrigerant evaporates outside the pipes. The state-of-the-art heat exchange pipes, internally and externally finned, together with the distribution of refrigerant - both at the evaporator inlet and at the suction - guarantee the achievement of very high efficiencies.
Beyond this advantage, compared to dry expansion evaporators, the partialization of the load can be lower. Through the use of jet pumps (supplied as an option) it is possible to use the flooded / spray evaporators also for oil systems. The removal of the caps allows the cleaning of the bundle and therefore the preservation of efficiency over time.
Flooded evaporator
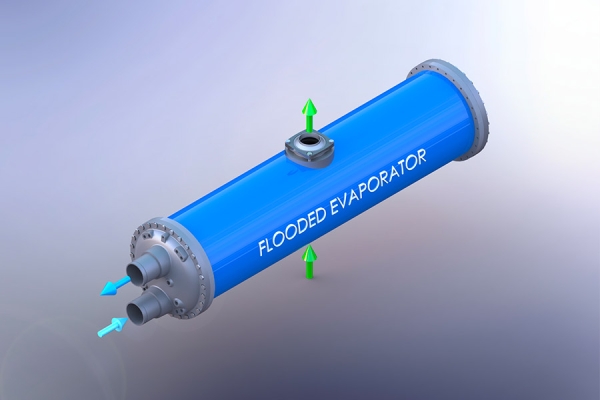
- Thermal powers from 50 kW up to 10 MW.
- Temperature approach down to 0.5K.
- Up to three refrigerant circuits; the tubes are expanded into intermediate tube plates, guaranteeing the seal between the circuits.
- Different configurations possible with 1, 2, 3 or 4 water passages.
- Absence of liquid entrainment thanks to the dedicated design of gas distributors for suction.
- Available optionals: elastomeric foam insulation, electric heaters, jet pump, Victaulic or flanged water connections, water filters.
- Regulation by means of refrigerant level control or subcooling temperature (liquid line).
Flooded evaporator 406
Flooded evaporator 508
Flooded evaporator 610
Flooded evaporator 711
Spray technology
Initially used for compact evaporators, the use of spray technology was subsequently implemented on S&T flooded evaporators.
Depending on the geometry, the saving of the refrigerant charge ranges from 50% up to 70%, compared to a flooded solution of the same size and performance.
The low level of the refrigerant allows it to be used easily even with screw compressors, as the oil concentration is relegated to a smaller amount of liquid and therefore easier to tap through the jet pumps.
The non-flooded area of the bundle also allows the spray evaporator to be used as a liquid receiver, as it can accommodate tens of kg of extra refrigerant without undergoing changes in efficiency.
The experience gained has made it possible to apply spray technology even to larger models. Environmental regulations impose increasingly stringent limits therefore reducing the amount of refrigerant is a big advantage, especially for large volumes.
To date, the revision of the project is available with the ESWT spray top version: the liquid refrigerant inlet positioned at 45 ° above the center line saves an additional charge of refrigerant and reduces the space required at the base of the exchanger.
Spray evaporator
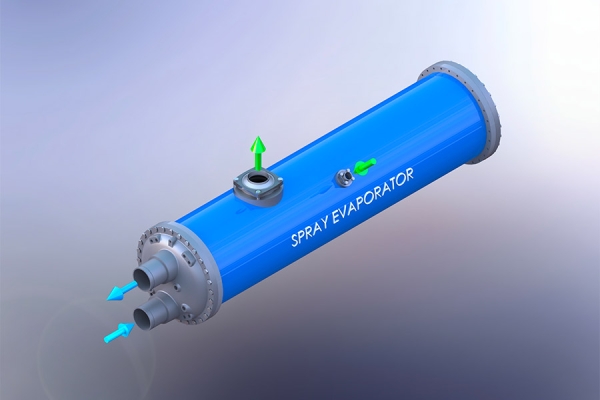
- Refrigerant charge down to 70% less compared to an equivalent flooded solutio.
- Version with liquid inlet from above (top feeding), optimizing the lower spaces.
- Performances, geometries and configurations such as flooded evaporators.
- High efficiencies and temperature approaches < 0.5K can be achieved with spray technology too!
Dual circuit spray evaporator
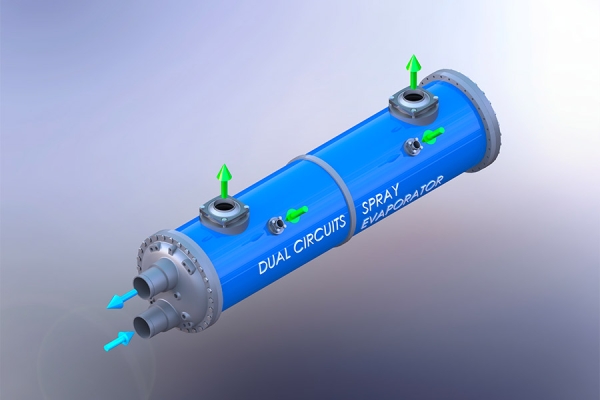
- Two independent cooling circuits to better track changes in cooling demand and increase system reliability.
- In case of circuit failure, the side that has remained in operation can still provide sufficient cooling until it is restored.
Compact CSF and CCF heat exchangers
The idea of a water-condensed refrigeration unit, compact, efficient, reliable and easy to maintain, found concreteness with the compact CSF and CCF heat exchangers.
The modular configuration (for redundancy or for capacity increase), the small footprint suitable for lifting in industrial goods lifts, the shell iron casing and the hinged caps to be able to inspect and clean the tube bundle are just some of the strengths of the our compact.
Usable with both oil-free and screw compressors, the compact heat exchangers - tested for a design pressure of 18 bar - can be used with HFC, HFO and propane refrigerants.
Compact flooded evaporators and condensers
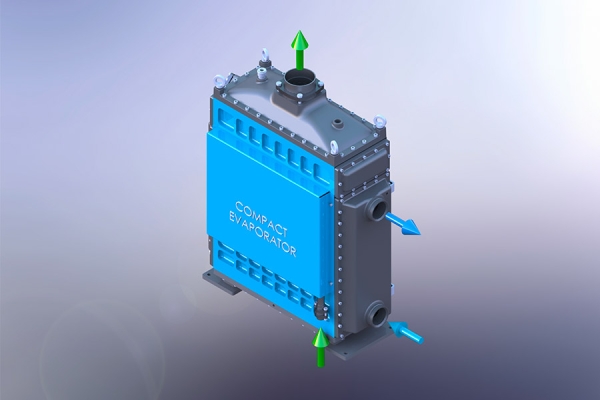
- Ideal for reduced spaces: compact volume 1300x1020x383 mm.
- Ideal for naval installations (without roll and pitching problems).
- Modular.
- 1K approach temperature with 300kW of cooling capacity.
- State-of-the-art high-efficiency tubes.
- Built-in intermediate exchanger to achieve additional subcooling at liquid line and suction superheat.
- Very low refrigerant charge required (75 kg for an oil-free chiller consisting of compact evaporator and condens).
- Possibility of having any number of water outlets as needed, according to the required ΔT in/out.
- Cleaning the tube bundle on the water side is possible WITHOUT the need to disassemble the water system, thanks to the hinged caps.
You need more information? Contact us!

Shell and tube heat exchangers for heat rejection up to 12 MW
Heat recovery possibility (partial or total) in the same shell.
Medium or high efficiency condensers, even for marine application!
In the recent decades Wieland Provides has designed flooded condensers suitable to cover any need: from the most compact dimensions to models able to dispose of the highest powers so far required in the field of industrial and process refrigeration; from cost-optimized single-pass counter-current solutions up to highly efficient 2 or 4 water pass models.
Some characteristics of our condensers:
- State-of-the-art heat transfer tubes, internally and externally finned, allow for more compact heat exchangers.
- Headers can be removed so to clean the tube bundle and therefore preserve the efficiency over time.
- Heat rejections from 50 kW up to 12 MW.
- Temperature approach as low as 0.5K.
- Different diameters and types of heat transfer tubes available
- Different shell side configurations: ‘standard’ with refrigerant distributor (TEMA X), counter-current (TEMA E), 2 liquid outlets (TEMA J12), etc.
- Up to three refrigerant circuits; the tubes are expanded into the intermediate tubesheets, guaranteeing the seal between the circuits.
- Different configurations available with 1, 2, 3 or 4 water passages.
- Marine construction available in cupronickel (CuNi90 / 10 tube bundle, plated tube sheets, ceramic treatment on the caps and sacrificial anodes) or titanium.
- Optional configurations for total heat recovery (2 water circuits side by side) or partial recovery (second water circuit using the desuperheating zone).
Condenser
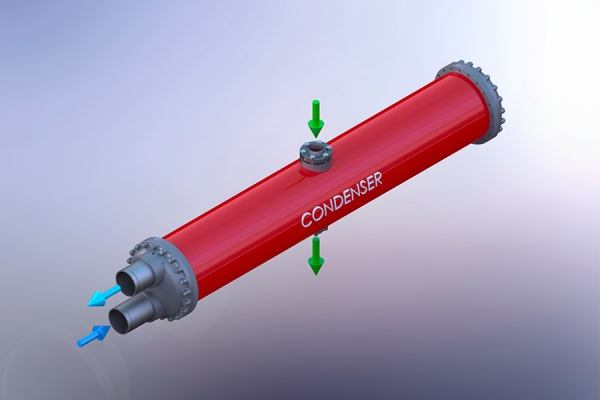
- Refrigerant inlet and oulet in central position
- Refrigerant gas distributor guarantees as high as possible efficiency of the heat transfer tubes
Standard condenser 219
Standard condenser 273
Standard condenser 356
Standard condenser 458
Standard condenser 508
Standard condenser 610
Counter-current condenser
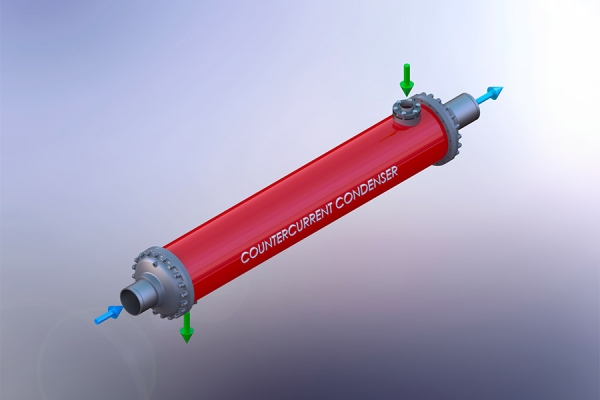
- Refrigerant inlet and oulet at the extreme edges and in counter-current with water flow, in order to take full advantage of the temperature profile
Countercurrent condenser 219
Countercurrent condenser 356
Countercurrent condenser 273
Countercurrent condenser 458
Dual refrigerant circuits condenser
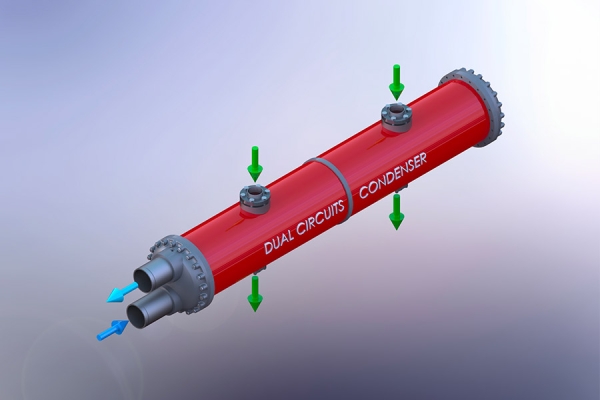
- Two independent refrigerant circuits so to follow the demand of the heat rejection and to increase the reliability of the system.
- In case of failure of one circuit, the working one will guarantee the partial operation until it is restored.
Reversible condenser
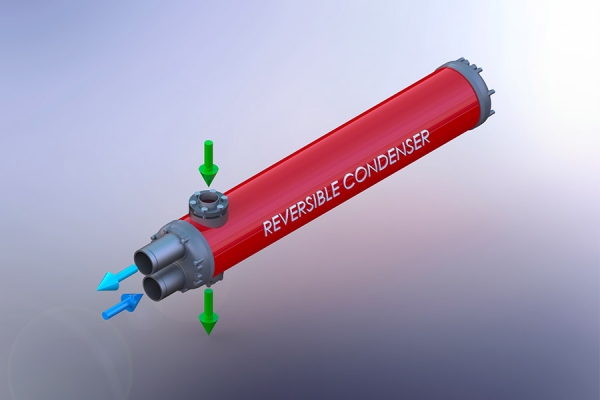
- Coming from the need to have a reversible flooded condenser, the CB.RV family combines the heat transfer efficiency in condensation with the possibility to use the same heat exchanger for defrosting cycles (shell side evaporation with inversion of the refrigerant cycle).
- This configuration is appliable to the different sizes of the standard condenser models, after verification by the Technical Department.
Desuperheater
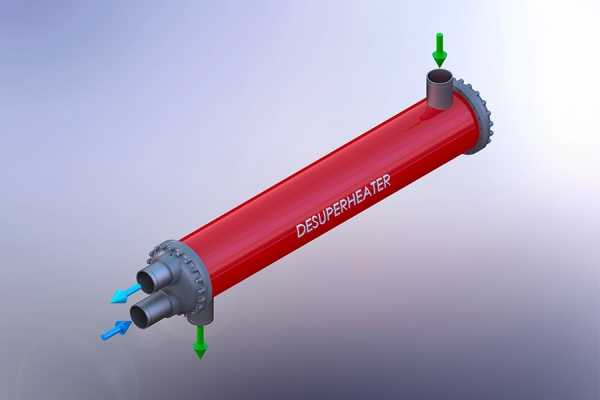
- The construction is similar to the condenser one; the desuperheaters are the best solution to achieve a heat recovery.
- The low pressure drops on the refrigerant side allow to use the sensitive heat without compromising the efficiency.
Compact condenser
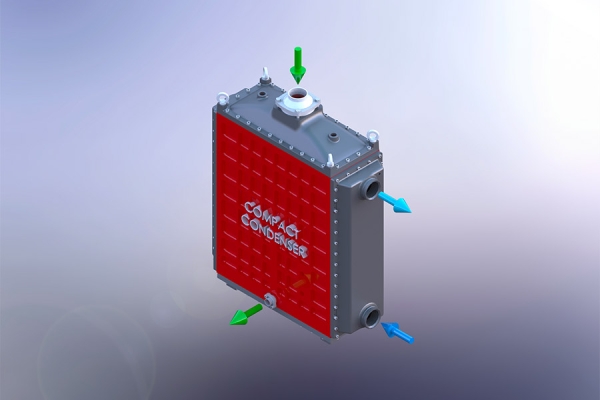
- Ideal for reduced spaces: compact volume 1300x1020x383 mm
- Ideal for naval installations (without roll and pitching problems)
- Modular
- 2K approach temperature with 350kW of heat rejection (R134a, oil-free).
- Very low refrigerant charge required (75 kg for an oil-free chiller consisting of compact evaporator and condenser).
- Possibility of having any number of water outlets as needed, according to the required ΔT in/out.
- Cleaning the tube bundle on the water side is possible WITHOUT disassembling the water system, thanks to the hinged header.
You need more information? Contact us!
A high class oil separation in refrigerant circuits is beoming more and more important
OSVM Oil separator vertical
With in-built oil reservoir. Capacity up to 700 kW.
Height : 1140mm
High efficiency oil separator with 3 step separation.
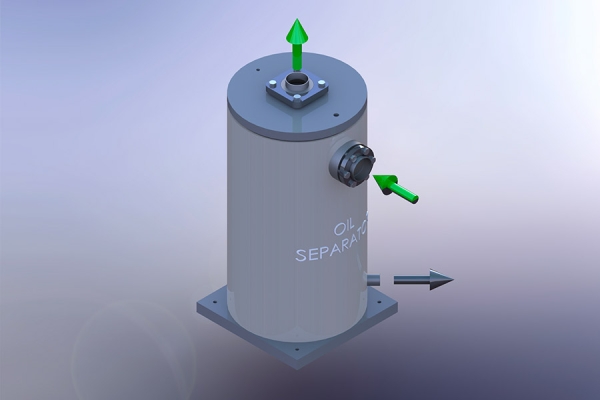
Oil separators are supplied with:
- Flanges
- Heaters
- Sleeve for sensor
- Sight glasses
- Oil outlet with Rotalock valve
- Separate valve for oil drain
- 1 3/4” thread for level sensor an optical level sensor
- 1 3/4” Rotalock optical level sensor is available as accessory
- Refrigerants HCFC and HFC
This oil separator eliminates the majority of the oil flow in the discharge gas. The oil flow through the system is very low. Oil carry-over coming out of the separator is less than 1 percent. Depending on the application 500 ppm carry-over is achievable. After the 4 step separation, oil is stored in the reservoir. Heaters keep the reservoir refrigerant free. Useable for flooded evaporator applications and for mono and multicompressor refrigeration systems.
OSHM oil separator horizontal
For direct oil return. Capacity up to 700 kW.
High efficiency oil separator with 3 step separation.
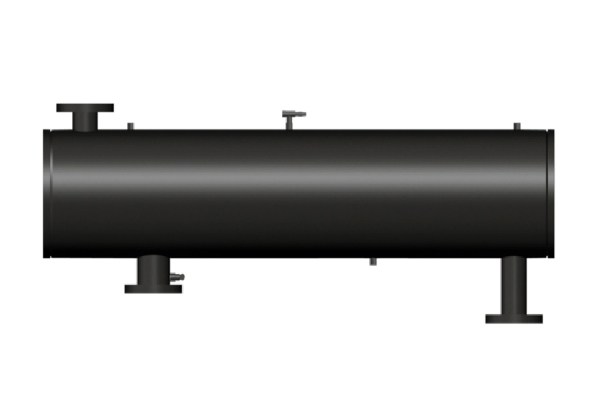
The oil separator are supplied with:
- Flanges
- Sleeve for hot gas outlet
- Oil outlet with ¾” flare valve
- Separate oil drainage tank
- 1 3/4” thread for level sensor
Accessories:
- Float valve
- Venturi nozzle
- ½” NPT optical level sensor
- Refrigerants HCFC and HFC
This oil separator eliminates the majority of the oil flow in the discharge gas. Depending on the application 500 ppm carry-over is achievable. This oil separator is for Scroll, Reciprocating compressors and for Compact screw with integrated oil separator. The oil separator has only a small volume of oil. This part is made for direct oil return. Especially for flooded evaporator application.
OSVF oil separator vertical
With coalescing cartridge. Capacity up to 350 kW.
Height : 785mm
Very high efficiency coalescing oil separator with 4 step coalescing filter.
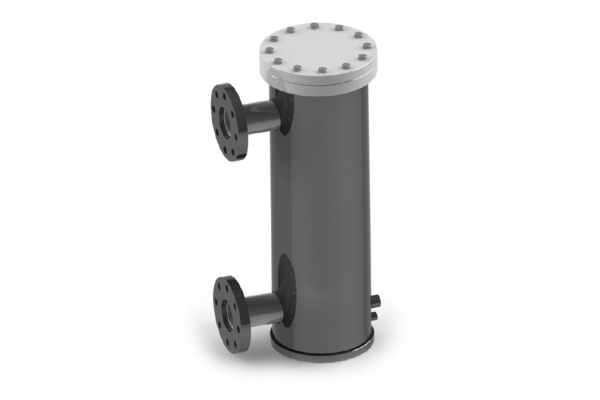
With this filter, liquid drops can be separated out of aerosols.
Oil Separators are supplied with:
- Flanges
- Sleeve for optic level sensor
- Oil outlet with ¾” flare valve
- Easily replaceable coalescing cartridge
Accessories:
- External float valve
- Venturi nozzle
- Capacity up to 350 kW
- Refrigerants HCFC and HFC
This oil separator eliminates the majority of the oil flow in the discharge gas. Depending on the application 10 ppm carry-over is achievable. This oil separator is for Scroll or Reciprocating compressors and Compact screw compressors with integrated oil separator. In this case, the filter can be used as a second step filtration with direct oil return. Especially for flooded evaporator application.
OSVMF combined
Oil separator vertical. Capacity up to 700 kW.
Height : 2000mm
Very high efficiency coalescing oil separator with 4 step coalescing filter.
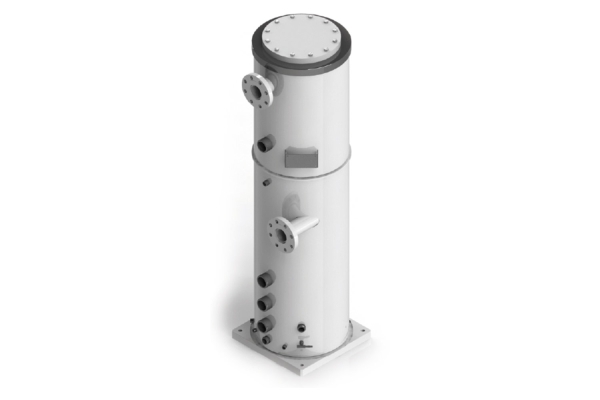
In the coalescing filters, liquid drops can be separated out of the aerosols.
The oil separators are supplied with:
- Flanges
- Heaters
- Sleeves for sensors
- Sight glasses
- Oil outlet with Rotalock valve
- Separate valve for oil drain
- 1 3/4” thread for level sensor
- Oil outlet with 1¾” Rotalock valve
- Easily replaceable coalescing cartridges
- Oil reservoir included
Accessories:
- External float valve
- Venturi nozzle
- Refrigerants HCFC and HFC
This oil separator eliminates the majority of the oil flow in the discharge gas. Depending on the application 10 ppm carry-over is achievable. This oil separator is for Scroll, Reciprocating compressors, or screw without oil separator. Useable for mono and multicompressor refrigeration systems.
You need more information? Contact us!

Already know your search term? Then go ahead and use our full text search. You will get a list of all relevant results.